HOW KOKBAN AUTOMATION HELPED PRINCIPAL GLOBAL SERVICE TO BECOME A SMART BUILDING :-
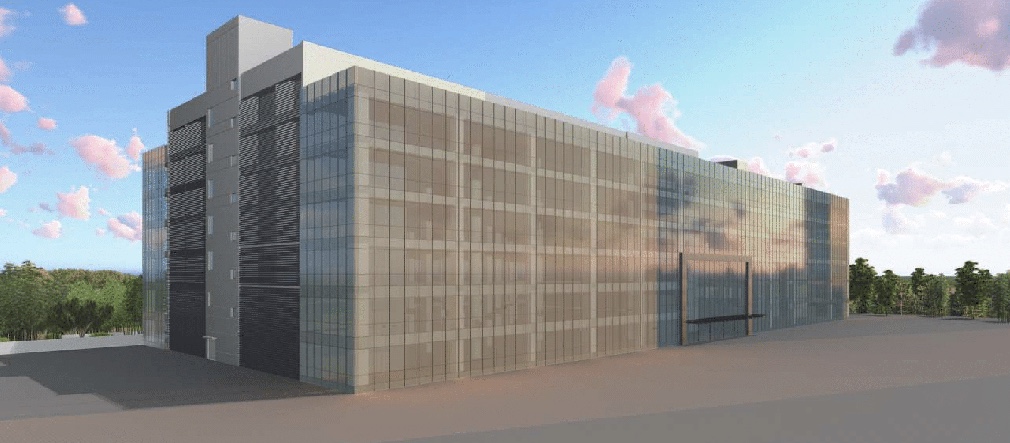
16th Jan 2020 | Prashik B Bansod
“It’s not the Beauty of the Building you should look at; It’s the construction of the foundation that will stand the test for the time.”
– David Allen Coe
Kokban Automation piloted it’s PLC based Building Management System solution across the Mechanical and Electrical component in PGS.
With the Globalization of Indian Industries and Construction segments and being made to compete against their Global Counterparts. It has become ultimate for Indian construction industries to adapt the new technology.
A Building Management System (BMS) is a crucial component to any infrastructure facility. It allows for centralized management of critical infrastructure equipment, and ensures operations are being run securely and efficiently.
The PGS PLC Based BMS Project is concerned with the Implementation of Safety features in the Building with the Powerful combination of Programmable logic Controller aided with SCADA end monitoring and control. This PGS Project can host high end technology in the equipment and large number of working and non working staff, so it is important to maintain the building properly and effectively. These facilities need proper climate control, fire suppression and backup power at every site that has physical security. Each of these systems needs to be monitored and maintained through a Building Management System. The BMS is backed up by redundant controller, and provides monitoring and alerts to ensure all aspects of the system are operating correctly. When considering a BMS, it is important that they comply with ASHRAE TC 7.0 and 9.0 standards for A1 environments and have a portal for customers’ views of the environment.
The DDC is best left for building automation and management systems where input output switching frequencies are low and future modification of control code are less frequent. In contrast, in an Industrial Control Environment and Large Buildings like manufacturing plant and Data Centre, control code is changed often, input and outputs are more likely to switch at a higher rate. So a PLC is best suited for that application. A computer (DDC) will have larger operating system which bogs down speed, increases complicity which reduces reliability in the industrial environment. Which is why the PLC was invented in the first place.
Since the invention of the PLC, processing speeds of computers have increased greatly, but there is still that complicity and reliability issue. For building control, a PLC would be better (more reliable and lower life cycle cost), but the initial investment in industrial grade PLCs is difficult for building automation designers to cost justify.
The Building Management System in PGS monitors each area in the following ways:
System Architecture The Components of PLC are The Central Processing Unit, Input/output (I/O) section, Power Supply, The Programming Device. An open architecture of PLC design allows the system to be connected easily to devices and programs made by other manufacturers. The PLC activates its output terminals in order to switch things on or off. The decision to activate an output is based on the status of the system’s feed-back sensors and these are connected to the input terminals of the PLC. The decisions are based on logic programs stored in the RAM and/or ROM memory. They have a central processing unit (CPU), data bus and address bus.
Communication Advantage Enhanced RS-232 port (includes 24V dc power for network interface devices). 4800; 9600; 19,200 baud rates. RTS/CTS hardware handshake signal Connection to DH-485, Device Net and Ethernet networks through the 1761-NET-AIC, 1761-NET-DNI, 1761-NET- ENI and1761-NET-ENIW interface modules. Connection to modems for remote communications
Power distribution must be consistent and clean once it reaches the computer equipment. The system helps ensure there are no power surges or inconsistent “spikes” of power that could damage the equipment. It also provides alerts to system managers if there are any power failures, surges or other issues with the power system.
UPS Generating the power distribution report for an hourly basis and integrated with the critical alarm.
WLD having the capability to detect the leakage on each and every floor and detect the leakage on exact distance wise.
Temperature control is vital for any infrastructure. Likewise in the PGS, the humidity needs to remain at 45 percent, because too much can damage the equipment and cause it to fail. The temperature needs to be consistent between 21 and 25 degrees, and can be adjusted or have circulation added as necessary by the BMS. Smoke fire damper high sensible are integrated with the HVAC system.
HVAC integrated with AHU, High sensible unit, Smoke fire Dampers and the VRF. 750 devices of HVAC are integrated and operated individually through the BMS monitor screen.
The fire suppression component uses a Very Early Smoke Detection Apparatus (VESDA) tied to the Building Management System to alert operators or sound an alarm if there is a potential fire. VESDA & NOVEC generating the loggoing and reporting daily and monthly basis.
A Building Management System can help operators monitor the facility from any location, on any device. This allows the center manager to be proactive if there’s ever an issue with part of the system instead of taking a reactive approach.
If there is ever an alarm for a system failure or issue, a facility engineer is notified and can immediately go to the site and resolve any possible problem. Some issues, such as temperature control, can be fixed through automation, so the engineer or manager does not need to return to or be at the site.